In the previous article we saw how, despite being a rather young material (160 years since the first forms of cellulose and 70 years since Natta’s synthesis of polypropylene, which gave the industry its real breakthrough) plastic has permeated every aspect of our daily lives.
This is because plastic has unique characteristics and is extremely versatile: it can be used in areas where its function is exhausted in a few days (packaging) but also in applications where its performance must be guaranteed for more than 50 years (buildings).
How many types of plastic are there and which are the most common?
Plastics are a plural reality, which is why it is more correct to speak of plastics rather than plastic: i.e. a wide variety of polymers, each with their own distinctive characteristics, properties and fields of application.
Following the DIN 7728 and 16780 standards, as well as the ISO 1043/1 international standards, each plastic material is assigned a unique identification code.
However, it is also necessary to make an initial distinction of plastics into two families: thermoplastic and thermosetting materials.
Thermoplastic materials are a family of plastics that can be melted when heated and can be hardened when cooled. These properties are reversible, which means that thermoplastic materials can be reheated, formed and hardened. Examples of thermoplastic materials are polyethylene, polypropylene, polycarbonate, polybutylene terephthalate, polyamides, etc.
Thermosetting materials are a family of plastics that undergo a chemical change when heated, creating a three-dimensional structure. After being heated and formed, these plastics cannot be melted and formed again.
Examples of thermosetting materials are polyurethane, silicone, methacrylic resin, vinylester, etc.
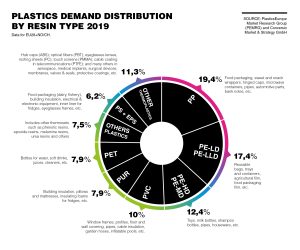
Fig. 1 Distribution of plastic demand by resin type 2019
Source: PlasticsEurope Market Research Group (PEMRG) and Conversio Market & Strategy GmbH
Quali sono i settori in cui viene impiegata la plastica, in Europa?
What are the sectors in which plastics are used in Europe?
60% of plastics are used in two sectors: packaging (39.6%) and construction (20.4%) The third sector with the highest demand for plastics is the automotive sector (9.6%).
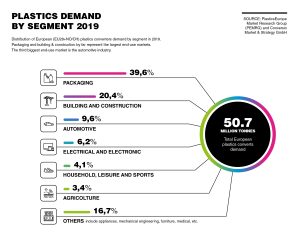
Fig. 2 Plastics demand by sector
Source: PlasticsEurope Market Research Group (PEMRG) and Conversio Market & Strategy GmbH
What types of plastics does FITT use?
For more than 50 years, FITT has been manufacturing pipes, hoses and systems for the flow of liquid, gaseous and solid substances for various application sectors: gardening, swimming pools, construction, nautical, infrastructures and much more.
Each solution is designed for maximum performance in terms of durability, yield and operability, and is manufactured with a specific chemical formula that entails the use of certain types of plastic.
PVC, polyolefins (polypropylene and polyethylene) and thermoplastic elastomers are the types most commonly used by FITT for its products.
Thanks to its resistance to mechanical stress in both hot and cold conditions, its intrinsic non-flammability and the fact that it can be specifically formulated for contact with drinking water and chemically aggressive substances, rigid PVC is used in the production of pipelines for construction, sewage and waterworks applications.
The high flexibility, weather resistance and versatility of flexible PVC make it ideal for the production of hoses for technical, liquid foods and gardening applications.
In addition, in both its rigid and flexible form, PVC is easily recyclable: it can be reused in production processes to generate new products, eliminate waste and reduce environmental impact.
Due to its light weight, chemical resistance properties and the possibility of being made fireproof, antibacterial and antistatic, polyethylene is also widely used in the production of pipelines for the construction industry, although in less demanding applications.
Thanks to its chemical inertness and ease of bonding with thermoplastic elastomers, polypropylene is ideal as a structural material in spiral hoses for technical and food applications.
Thermoplastic elastomers represent the new frontier for technical hoses and garden hoses: on the one hand, they retain the thermoplastic aspects that make them completely recyclable; but also, they can achieve resistance and elasticity characteristics comparable to those of rubber.
These special hybrid blends of rubber and polypropylene include styrene-based and pre-vulcanised rubber-based thermoplastic elastomers (TPE). The former are particularly suitable for transporting drinking water and liquid foods, while, together with thermoplastic polyurethane elastomers (TPU), the latter are ideal for medium-heavy-duty applications requiring anti-abrasive properties and resistance to prolonged mechanical stress at higher temperatures.
Ethylvinyl acetate (EVA) , another thermoplastic elastomer, is used in two different applications: due to its low density, which allows it to float, it is used in swimming pool cleaning pipelines , while its transparency and ability to contain the heat generated inside the greenhouse by the sun rays, make it suitable for the manufacturing of greenhouse films.
Finally, polyester is widely used in the textile reinforcement of hoses. PET yarns can be easily bonded to all plastics, and thanks to their strength they guarantee the pressure resistance of hoses.